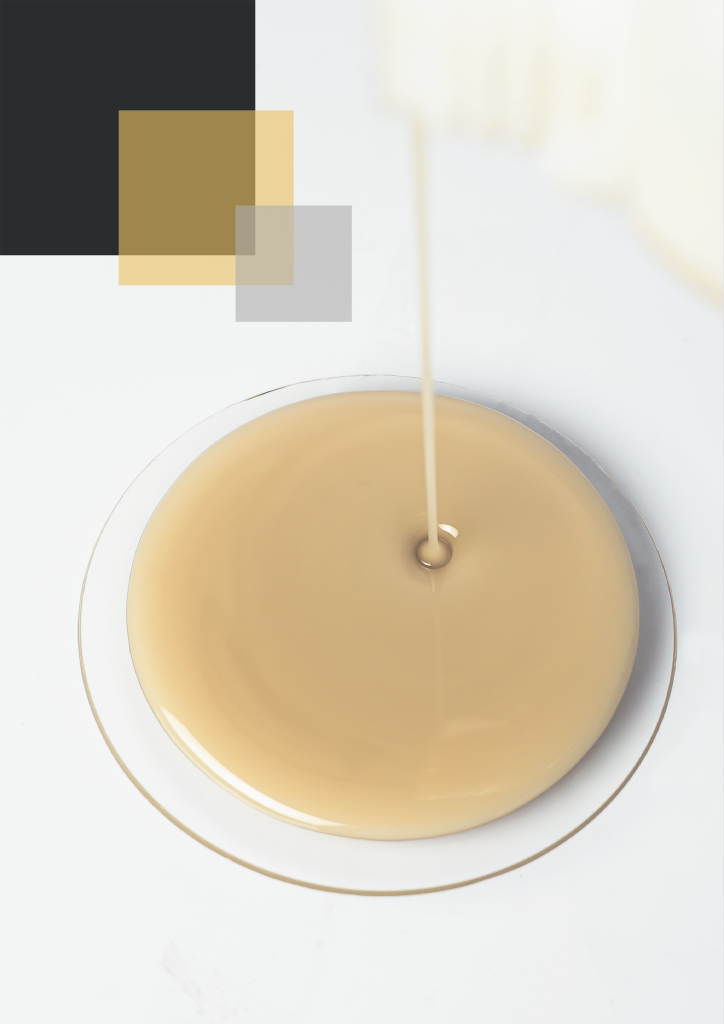
Преимущества системы
- Наполненная безусадочная полиэфирная смола
- Позволяет сразу набирать толщину до 5.5 мм
- Превосходная размерная стабильность
- Однокомпонентная система (отверждение MEKP)
- Высокое HDT
Компоненты системы OPTIMOLD II
Polycor Tooling Gelcoat
Модифицированный изофталевый полиэфирный гелькоут. Наносится при помощи распылителя (версия PA) или при помощи кисти (версия BR). Обеспечивает прочное, глянцевое и износостойкое покрытие.
NORSODYNE H 44281 TA
Изофталевая смола с повышенной стойкостью к химическому воздействию и высокой температурой тепловой деформации (HDT). Используется для пропитки первого армирующего слоя (стекловуаль), идущего после гелькоута (skin-coat).
OPTIMOLD II
Наполненная тиксотропная полиэфирная смола с содержанием низко-усадочных добавок. Позволяет набирать ламинат большой толщины (от 4.3 мм до 5.5 мм ) за один цикл формования. Обеспечивает матрицам превосходную стабильность размеров.
Характеристики не отвержденной смолы
Характеристика | Условие | Единица Измерения | Значение |
Плотность | 23оС | г/см3 | 1,27 – 1,33 |
Содержание твердых веществ | 15 минут | % | 65-70 |
Вязкость | 23оС, Шпиндель 3, 50 об/мин | мПа.сек | 1100-1600 |
Время гелеобразования | Катализатор с низкой активностью | Мин | 18-22 |
Пик экзотермы | 25оС, В объеме 250 мл, 1.5% MEKP | Мин | 25-35 |
Температура экзотермы | 25оС, В объеме 250 мл, 1.5% MEKP | оС | 170-190 |
HDT | 3 часа при 80оС + 2 часа при 120оС | оС | 140 |
Предел прочности | 16 часов при 40оС | МПа | 92 |
Относительное удлинение при разрыве | 16 часов при 40оС | % | 1,8 |
Этапы производства матрицы
1. ОЧИСТКА И НАНЕСЕНИЕ РАЗДЕЛИТЕЛЯ НА МАСТЕР-МОДЕЛЬ
- Очистите поверхность мастер-модели при помощи специального матричного очистителя. Очиститель может быть как на водной основе, так и на основе растворителя.
- Нанесите разделитель на поверхность мастер модели согласно TDS. Разделитель может быть на восковой основе (мягкой или твердой), полупостоянной, фторполимерной (жидкой или аэрозольной), пва. Для некоторых разделителей может потребоваться грунт/порозаполнитель.
- Обычно разделители наносятся вручную, для восковых используется поролоновая губка-аппликатор, для полупостоянных или фторполимерных рекомендуется использовать специальные салфетки Scott Shop.
- Тщательно перемешайте необходимое количество гелькоута перед нанесением, вручную или при помощи инструмента. Дайте отстояться 10-15 минут для удаления воздушных включений.
- Подготовьте необходимое количество катализатора MEKP (Butanox M-50) согласно TDS. Не используйте более 3% и менее 1,2% катализатора, 1,8% – рекомендуемое значение.
- Для версии гелькоута BR используйте качественные плоские кисти с мягким ворсом и плотной металлической обвязкой, во избежание попадания выпавших ворсинок на наносимую поверхность.
- Для версии гелькоута PA используйте пистолеты с дюзой 2,5 – 4,8 мм, при рабочем давлении 4-6 Атм. Наличие влагоуловителя в воздушной системе обязательно.
- Нанесите 1 слой гелькоута на поверхность мастер-модели.
- Выдержите гелькоутную пленку до состояния “на отлип” (когда гелькоут при касании пальцем липкий, но не пачкается). Как правило, это время не превышает 1-го часа.
- Нанесите 2 слой гелькоута (желательно контрастного цвета).
- Выдержите гелькоутную пленку до состояния “на отлип”.
2. НАНЕСЕНИЕ ЗАПОЛНЯЮЩЕЙ ПАСТЫ FSP-HV 1534
- Данный этап необходим при наличии на поверхности мастер модели прямых углов, поднутрений и т.п., мест в которых с большой долей вероятности не уложится армирующий стекломатериал, мест в которые не может попасть прикаточный валик.
- Применение заполняющей пасты после гелькоута, позволяет упростить геометрию формуемой матрицы и ускорить последующие этапы изготовления, улучшить качество композита, за счет снижения вероятности образования воздушных включений в сложных местах.
- Подготовьте необходимое количество катализатора MEKP (Butanox M-50) для пасты FSP-HV 1534 согласно TDS. Не используйте более 2% и менее 0,6% катализатора.
- Пасту можно наносить кистью, шпателем, конвертом. Не наносите за один этап более 20-ти мм толщины.
- Выдержите пасту до состояния “на отлип” (когда паста при касании пальцем липкая, но не пачкается). Как правило, это время не превышает 1,5 часа.
3. ФОРМОВАНИЕ ЛИЦЕВОГО СЛОЯ
- Лицевой слой, идет следующим после гелькоута/заполняющей пасты. Его назначение – это устранение копир-эффекта от стекловолокна, создание барьерного слоя с повышенными физико-механическими характеристиками.
- Подготовьте необходимое количество катализатора MEKP (Butanox M-50) для смолы Norsodyne H 44281 TA согласно TDS. Не используйте более 2,5% и менее 1% катализатора, 1,5% – рекомендуемое значение.
- Предварительно ракроите стекловуаль E-FM 30, с плотностью 30 грамм на квадратный метр, при сложной геометрии минимизируйте стыки вуали, нахлесты более 5-ти мм не желательны.
- Смешайте смолу с катализатором, обильным слоем нанесите смолу на всю поверхность гелькоута. Гелькоут должен быть в состоянии “на отлип”.
- Уложите стекловуаль на смоченную поверхность, немного прибейте ее к поверхности при помощи кисти.
- Обильным слоем при помощи кисти нанесите смолу на стекловуаль.
- При формовании уделяйте внимание углам и поднутрениям, не допускайте излишнего скопления смолы.
- Выдержите слой до состояния “на отлип”. Как правило, это время не превышает 1,5-2 часа.
4. ФОРМОВАНИЕ ОСНОВНЫХ СЛОЕВ
- Тщательно перемешайте необходимое количество матричной смолы Optimold II с небольшим запасом при помощи инструмента. Дайте отстояться 3-5 минут для удаления воздушных включений.
- Для увеличения рабочего времени на формование, рекомендуется предварительно разбить общее количество матричной смолы на те количества, которые хватает ровно на 1 армирующий слой.
- Подготовьте необходимое количество катализатора MEKP (Butanox M-50) для матричной смолы Optimold II согласно TDS. Не используйте более 2% и менее 1% катализатора, 1,5% – рекомендуемое значение.
- Предварительно ракроите эмульсионный стекломат требуемой плотности, разложите слои в необходимой последовательности.
- Если при формовании используются стекломаты разных плотностей, то на первые слои рекомендуется укладывать стекломат с наименьшей плотностью.
- Формуйте послойно, с обязательной прикаткой каждого армирующего слоя при помощи прикаточного валика.
- Не рекомендуется за один цикл формования набирать ламинат более 6-ти мм.
- Если все условия формования выполнены правильно, то смола в процессе полимеризации и экзотермического пика изменит цвет на светло-бежевый.
- Спустя 24 часа после формования, рекомендуется прогреть матрицу согласно режиму, указанному в TDS.